Pneumatic Conveying Systems: Revolutionizing Material Transport
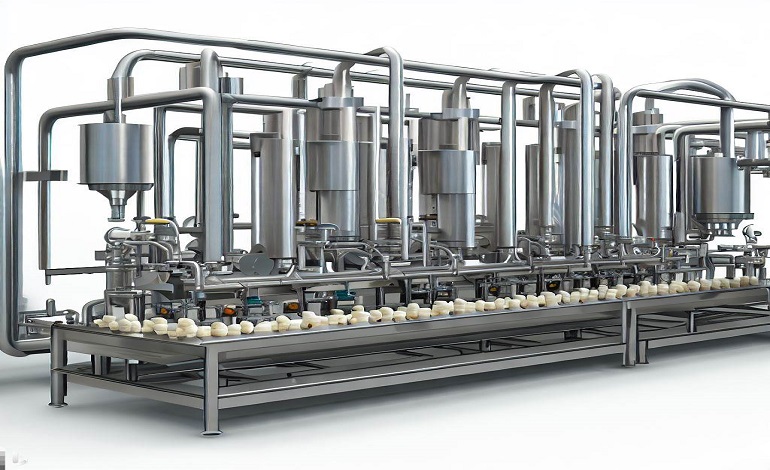
Introduction
Welcome to our comprehensive guide on pneumatic conveying systems. In this article, we will explore the fascinating world of these innovative systems that have revolutionized material transport across various industries. From the fundamental principles to their applications and benefits, we will provide you with in-depth knowledge to help you understand and appreciate the power of pneumatic conveying systems.
Understanding Pneumatic Conveying Systems
What are Pneumatic Conveying Systems?
Pneumatic conveying systems are advanced methods of transporting bulk materials using air or gas flow. By utilizing differential pressure, these systems move powders, granules, and other dry materials efficiently and reliably. They are widely employed in industries such as food processing, pharmaceuticals, chemicals, plastics, and mining.
Types of Pneumatic Conveying Systems
-
Dilute Phase Conveying: This system involves high-speed and low-pressure airflow to transport materials. It is suitable for lighter materials and can cover long distances.
-
Dense Phase Conveying: In this system, materials are conveyed at low velocities, allowing for better control and gentle handling. Dense phase conveying is ideal for heavy, fragile, or abrasive materials.
-
Vacuum Conveying: Vacuum-based systems utilize suction to transport materials. They are commonly used in applications where cleanliness and dust control are crucial, such as in the pharmaceutical and food industries.
Advantages of Pneumatic Conveying Systems
Pneumatic conveying systems offer numerous advantages over traditional mechanical conveyors. Let’s delve into some of the key benefits:
1. Seamless Material Transfer
With pneumatic conveying systems, material transfer occurs through enclosed pipelines, eliminating the risk of contamination or spillage. This ensures a cleaner and safer working environment, minimizing product loss and reducing cleanup efforts.
2. Flexibility and Versatility
Pneumatic conveying systems can be customized to meet the specific requirements of different industries. They can transport materials horizontally, vertically, or even at inclined angles, offering unparalleled flexibility in system design and layout.
3. Increased Efficiency and Productivity
By automating material handling processes, pneumatic conveying systems streamline operations, leading to increased efficiency and productivity. These systems can transport materials continuously, reducing manual intervention and optimizing workflow.
4. Dust-Free Operation
One of the significant advantages of pneumatic conveying systems is their ability to operate without generating dust. This is particularly critical in industries where maintaining a dust-free environment is essential for product quality and employee health.
5. Cost-Effective Solution
While the initial investment for installing a pneumatic conveying system may be higher than traditional conveyors, the long-term cost benefits outweigh the upfront expenses. Reduced maintenance requirements, energy efficiency, and improved productivity contribute to overall cost savings.
Applications of Pneumatic Conveying Systems
Pneumatic conveying systems find extensive use across various industries due to their versatility. Let’s explore some of the key applications:
1. Food Processing
In the food industry, pneumatic conveying systems play a crucial role in the transfer of ingredients, such as flour, sugar, spices, and additives. Their gentle handling capabilities ensure the integrity of sensitive food products, while the enclosed transport eliminates contamination risks.
2. Pharmaceutical Industry
Pharmaceutical manufacturing demands precision and stringent quality control. Pneumatic conveying systems offer the ideal solution for transporting pharmaceutical powders, excipients, and active ingredients, maintaining product purity and meeting regulatory standards.
3. Chemical and Plastics Industry
Pneumatic conveying systems are widely utilized in chemical and plastics manufacturing for handling materials such as resins, pigments, additives, and powders. Their ability to transport hazardous or abrasive substances safely and efficiently makes them invaluable in these industries.
4. Mining and Minerals
The mining industry relies on pneumatic conveying systems to transport various minerals and ores. These systems ensure the seamless movement of materials across long distances, even in challenging environments, contributing to improved operational efficiency.
5. Cement and Building Materials
In the construction sector, pneumatic conveying systems are instrumental in the transportation of cement, sand, fly ash, and other building materials. They facilitate the efficient and precise distribution of these materials, reducing waste and enhancing construction site productivity.
Choosing the Right Pneumatic Conveying System
When selecting a pneumatic conveying system for your specific application, several factors need to be considered:
-
Material Characteristics: Understand the properties of the materials you intend to transport, such as particle size, density, and flowability. This information will help determine the appropriate conveying system type.
-
System Capacity: Evaluate the required conveying capacity to ensure that the system can handle the desired material volume effectively.
-
Distance and Layout: Consider the distance and layout of the material transfer. Determine whether the system needs to transport materials vertically, horizontally, or both, and ensure the chosen system can accommodate these requirements.
-
System Control and Monitoring: Opt for a system that offers robust control and monitoring capabilities. Features such as automation, remote monitoring, and process optimization can enhance system performance and reliability.
-
Maintenance and Serviceability: Look for systems that are easy to maintain and service. Components that can be accessed easily for cleaning, inspection, and repairs contribute to smoother operations and reduced downtime.
Implementing Pneumatic Conveying Systems Effectively
To maximize the benefits of pneumatic conveying systems, consider the following implementation tips:
-
Collaborate with Experts: Work with experienced engineers or system integrators who specialize in pneumatic conveying. Their expertise can help design and optimize the system to suit your specific needs.
-
Regular Maintenance and Inspection: Establish a preventive maintenance schedule to ensure that the system operates at peak performance. Regularly inspect and clean the pipelines, filters, and other components to prevent clogs and ensure smooth material flow.
-
Training and Operator Knowledge: Train your operators thoroughly to understand the system’s operation, maintenance requirements, and troubleshooting procedures. Well-trained operators can identify and address issues promptly, minimizing downtime.
-
Continuous Improvement: Regularly review system performance and seek opportunities for improvement. Upgrades, technology advancements, and process optimizations can further enhance the efficiency and productivity of pneumatic conveying systems.
Conclusion
Pneumatic conveying systems have transformed the way materials are transported across multiple industries. With their ability to provide dust-free, efficient, and flexible material handling solutions, these systems have become indispensable for modern manufacturing processes. By understanding the different types, benefits, applications, and implementation considerations of pneumatic conveying systems, businesses can optimize their operations, minimize costs, and drive productivity to new heights.
Copyright 2023, Air Dynamics , All Rights Reserved | Design & Developed By Eonlogic